Australian grid operator Transgrid has partnered with German machinery manufacturer Zeck for the use of its innovative steel separation tech. Zeck’s machine can process electricity transmission lines into a recycle-ready state onsite. Previously, Transgrid sent old transmission lines offshore for this process at a much higher cost.
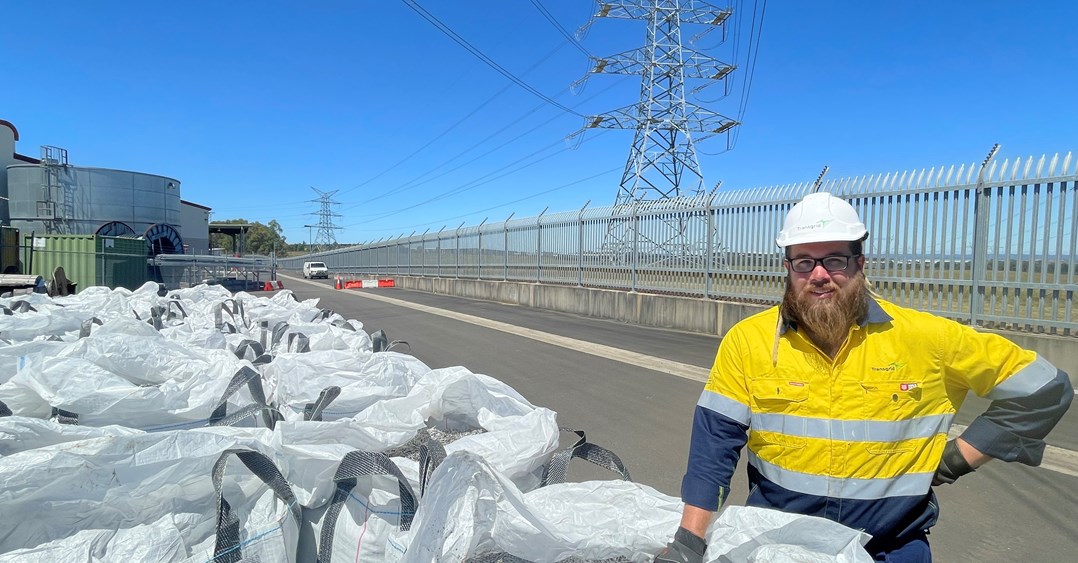
Transgrid Field Coordinator Mitch Coppock stands proudly with neat bags of recycle-ready transmission lines.
Image: Transgrid
Transgrid, the grid operator for the Australian state of New South Wales and Australian Capital Territory (ACT), has partnered with German manufacturer Zeck to use its ZECK AI/Steel Separator (ZAS), an innovative machine that enables the recycling of old transmission lines – providing significant cost and emissions reductions.
The network operator said that prior to the adoption of the ZAS technology, used conductors needed to be shipped overseas for the removal of the outer aluminum layer for recycling. The ZAS machine can do this on site – an innovation which Transgrid claims cuts 90% of the emissions involved in recycling conductors.
Transgrid also forecasts an improved return on its scrap metal recycling of up to AUD 3 million ($2.06 million) over the next three to five years.
By feeding conductors into the ZAS machine under tension, the previously outsourced task of removing the outer aluminum layer is now performed onsite and efficiently, with said aluminum cut into 30 mm to 70 mm pieces for easy smelting. At the other end of the ZAS machine, the undamaged conductor's steel core is wound onto a cable drum, also ready for recycling.
It was one of Transgrid's field coordinators, Mitch Coppock, who first pitched the idea of using the ZAS machine.
“Something like that hasn't been done in Australia before,” said Coppock. “Anything innovative we can do is very important in our industry especially anything that can have good long-term effects on the environment.”
It's an “everyone wins” situation, says Coppock, as Transgrid can get a return on its scrap metal three times higher than before, while “the environment wins with reduced emissions and local businesses benefit too as they get readily available and processed aluminum.”
The trial has already seen 40 km of conductors processed through the ZAS machine in Sydney, with each meter of conductor yielding approximately a kilogram of aluminum.
It has been a period of firsts for the network operator, which recently began trialing its first electric pickup truck among a 400-strong diesel vehicle fleet.